NFC STE was established from NSC KIPT divisions previously engaged in development of structural, neutron-absorbing, and nuclear materials for design of fuel rods, absorber rods, and fuel assemblies for reactors of different types and purposes. NFC STE specialists acquired their experience in design of nuclear fuel for nuclear facility cores during NSC KIPT developments as designers of and industrial engineers for absorber rods, fuel rods, and fuel assemblies for the following types of reactors:
-
heavy water reactors KS-150, TR-1000, where heavy water was used as the neutron moderator, carbon dioxide as the coolant, and metallic uranium as the nuclear fuel;
-
nuclear heating plants: AST-100, AST-500, and ARBUS (Arctic package plant) reactors with organic coolant and high-density fuel rods (primarily metallic uranium);
-
WWER-1000 and RBMK-1000 reactors – design of fuel rods with high-density fuel (metallic uranium-based alloys);
-
fast neutron reactors with gas coolants (BGR-300);
-
fast neutron reactors BRIG-300 with the dissociating N2O4 coolant;
-
different special-purpose reactors.
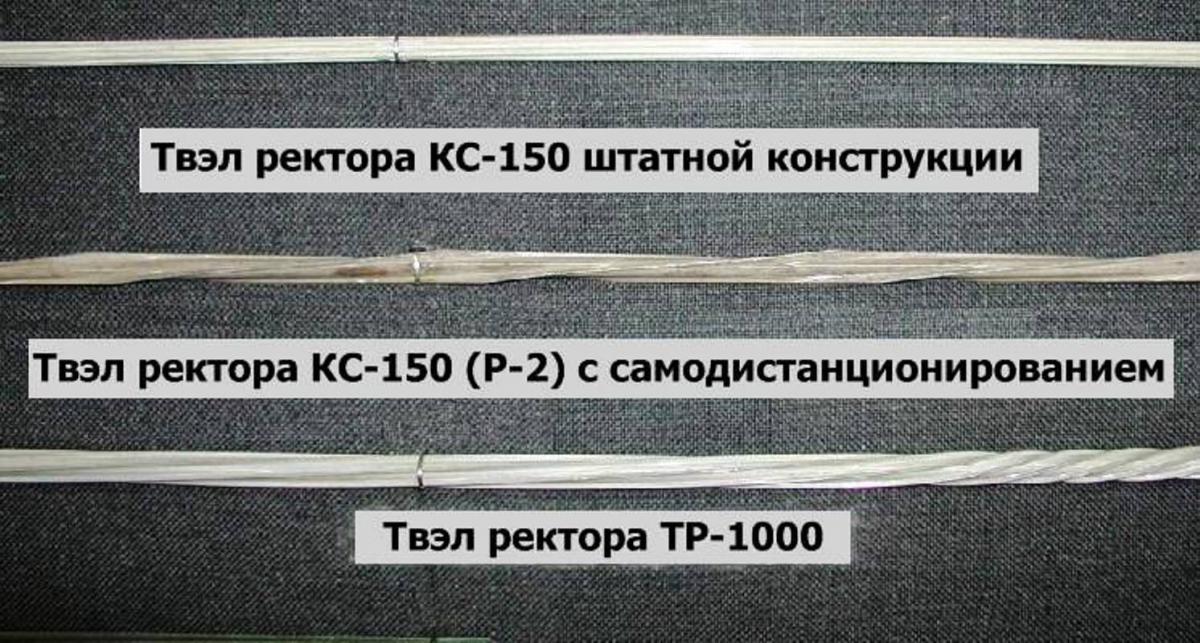 |
Fragments of three types of fuel assemblies for the heavy water KS-150 reactor
|
|
The results of these developments were used to develop fuel rods and fuel assemblies for the heavy water TR-1000 reactor and nuclear heating plants of the AST-100 and AST-1000 types.
Developments of Core Components for Nuclear Facilities
NSC KIPT developed fuel rods with metallic uranium fuel in zirconium cladding as direct replacement for the uranium dioxide fuel in WWER-1000 and RBMK-1000 reactors. The core consists of separate sections, where fuel has central void to compensate for fuel swelling. Fuel sections are separated so that leakage in any one of them does not result in contact with the neighboring sections' coolant. The fuel rods underwent reactor tests in the “World First NPP” up to a design burnup of 22 MWD/kgU. The tests were completed in 1985.
Design of the experimental WWER-1000 fuel rod with a partitioned uranium core
|
The design and manufacturing technology of dispersion matrix fuel was tested in a FA of the fast neutron reactor BRIG-300 with the dissociating N2O4 coolant. A similar design was developed for the fast neutron reactor BGR-300 with the helium coolant. Developments of 1970-1985.
Dispersion fuel for gas-cooled reactors
|
UO2 and UC fuel micro spheres with different coating materials, whose manufacturing technology was developed at NSC KIPT, can be used in the rods of fast neutron reactors and high-temperature helium reactors with pebble or prismatic fuel.
|
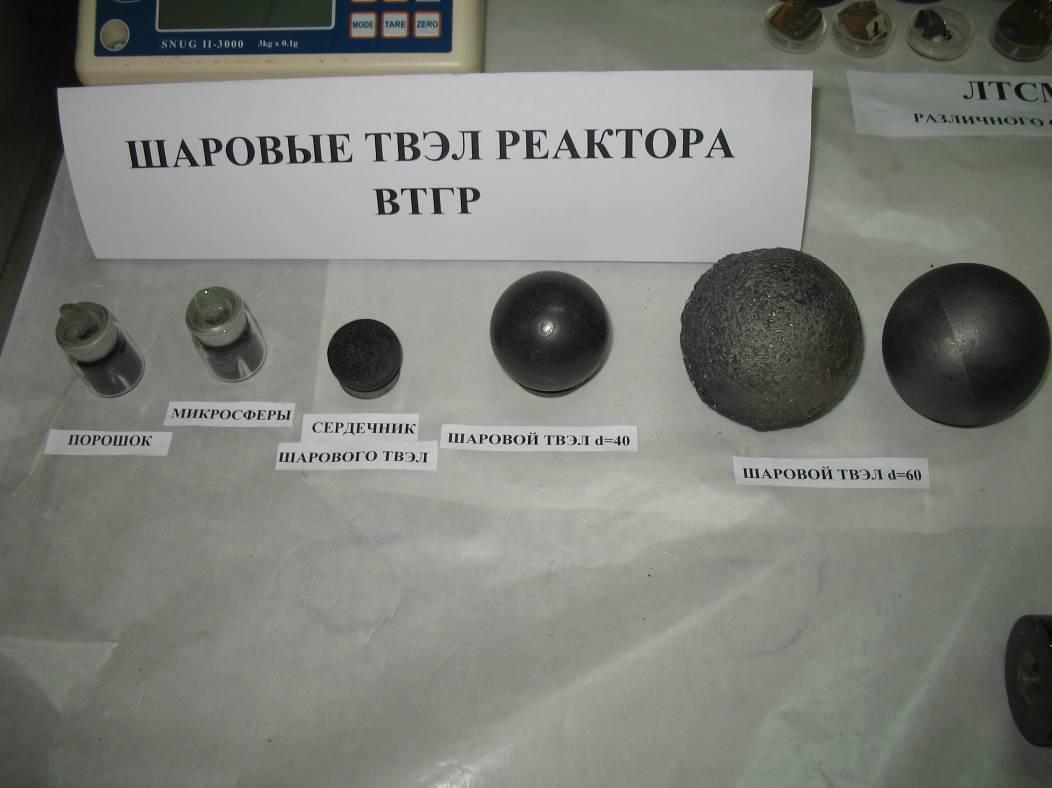
The use of fuel micro spheres in pebble fuel of the high temperature gas-cooled reactor
|
Development of fuel and absorber element designs and manufacturing options for reactors of different types and purposes was supported by comprehensive development of materials, designs and manufacturing technologies for materials of nuclear facility core components:
-
melting and production of rods from alloys of various composition based on metallic uranium;
-
treatment of metallic uranium through plastic deformation (pressing, drawing, and rolling) to obtain products shaped as solid or hollow rods, fuel micro spheres (Ø1 mm), and fuel pebbles with an internal hollow (Ø10 mm);
-
thermomechanical treatment of products made of metallic uranium and its alloys to create radiation resistant fuel rod cores with a specified structural state and phase composition and required texture parameters;
-
the elaborated processes of fuel rod sealing through welding include inert gas welding at high pressures (~100-200 atm.), electron-beam welding in vacuum, and resistance butt welding;
-
there were developed a number of bonded fuel rod designs and their manufacturing technologies;
-
there were developed a number of materials characterized by enhanced radiation resistance for the fuel rods operated in chemically aggressive environments;
-
there were developed destructive and nondestructive control methods to test absorber and fuel rods for failure tolerance and to determine their operation life based on out-of-pile tests;
-
there were developed heat treatment methods for zirconium alloys with niobium (fuel rod cladding tubes, RBMK and CANDU channel tubes ensuring their high radiation resistance in reactors);
-
there were developed designs and manufacturing technologies for absorber rods with hafnium for the WWER reactors characterized by enhanced operation life and reliability (safety). The work is underway to manufacture pilot samples and to test them for compliance with the design parameters;
-
there were developed manufacturing technologies for a number of bonded fuel rod designs;
-
absorber elements for dry storages of spent nuclear fuel were developed and are manufactured;
-
research was conducted on formation of the melt of core materials during the Chornobyl accident. The research on the melt of materials constituting cores of water-cooled and water-moderated reactors for severe beyond design-basis accidents continues.
Engineering Support for Nuclear Fuel Operation at Ukraine's NPPs.
-
Implementation of the Ukraine Nuclear Fuel Qualification Project (UNFQP) and establishment of the Center for Reactor Core Design (CRCD) with the main objective to implement advanced foreign technologies for core design and safety analysis;
-
Qualification of computer codes used for design and safety substantiation of the cores composed of the fuel provided by different vendors;
-
Support of Westinghouse fuel assembly operation at South Ukraine NPP Units 2 and 3;
-
Development of advanced fuel cycles pursuant to the contract with Westinghouse;
-
Development of the methodology for safety substantiation using 3-D neutron kinetic codes for WWER-1000 reactors and its concurrence with the Regulator;
-
Simulation of thermal hydraulic processes in reactors and dry storage facilities using CFD based codes.